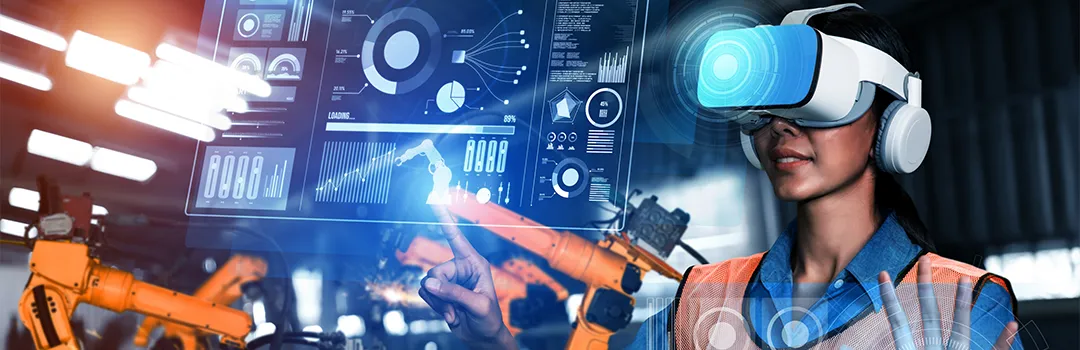
Trends in Manufacturing: Adapting to the New Skills and Talent Paradigm
Table of Content
- What is causing the talent shortage in manufacturing?
- Trends in manufacturing
- Which new skills will be required from the digitization perspective?
- ESG and DEI: Close monitoring required for sustainability and growth
- How can a leader strategize talent acquisition to cater to existing and future skill requirements?
- To conclude
The latest trends in manufacturing are significantly influencing how leaders address the changing talent strategy. Skill diversification in manufacturing is nothing new.
From the technology perspective, several waves of Industrial Revolution have transformed manufacturing in innumerable ways over the last 150-200 years. Much like its predecessors –the First(steam, mechanical production), Second (advent of electricity, division of labor, mass production), and Third (electronics and IT) Industrial Revolutions –the Fourth Industrial Revolution (cyber-physical systems or Industry 4.0) is disrupting workforce dynamics in manufacturing.AI, IoT, advanced analytics, high-tech robotics and cognitive automation are rapidly rendering several older job roles irrelevant.
To stay competitive, manufacturing companies need to adopt automation and technological advancements. This means reconfiguring the skills and talent diversification strategy.
But this is just one aspect.
Companies, today, are transforming from purely economic entities into entities with instincts and interests that go beyond financial gains. Amid growing social consciousness and regulatory pressures, sustainability, diversity, equity & inclusion (DEI) and environmental, social and governance (ESG) are fast making inroads into the echelons of leadership and C-suite.
The manufacturing leadership needs to rethink the talent acquisition strategy to stay relevant in the race. Skill supply or skill enhancement has transcended the conventional approach of recruiting from the same domain to fill the gap. Rising human-centricity has rendered talent acquisition fluid. Manufacturing companies require a workforce that cuts across domain-specific knowledge.
What is causing the talent shortage in manufacturing?
The growing requirement for newer skill sets has created a gap between the supply of talent and demand. According to the fourth skills gap study by Deloitte and The Manufacturing Institute in 2018, companies in the US manufacturing sector are staring at a projected talent shortage of 2.4 million workers over 2015 to 2025.
It would have been a lot simpler if the hunt for key talent was the only challenge.
Trends in manufacturing
As per Deloitte’s 2023 Manufacturing Industry Outlook, the manufacturing sector continued to strengthen in 2022, as it built on the momentum of the previous two years following the pandemic. While production capacity has been high, as is demand, there are significant challenges. These include shortage of labor, an uncertain economic environment, rising inflation, cost pressures, cyberattacks and supply headwinds.
To sustain the momentum, leaders need to not just embrace the disruption but also revamp their approach.
Manufacturers would be guided by 5 key trends:
- Continued investment in advanced manufacturing technologies for operational agility
- Adoption of broad-based talent management strategies to address and reduce voluntary exits. As the industry confronts labor shortage and a high workforce churn, talent models are shifting. Job openings continue to remain high. Voluntary exits outnumber layoffs. This, coupled with supply chain issues, could bring margins under pressure.
- Supply chain risk mitigation using advanced tactics
- Continued implementation of smart factory initiatives
- Growing focus on corporate social responsibility amid fast growth in the ESG landscape
Which new skills will be required from the digitization perspective?
According to global management consulting firm OliverWyman’s analysis, the impact of digitization will be felt along the entire manufacturing value chain; this includes indirect production functions, technical services and administration. From automation of production to game-changing innovations that power the industry (such as big data, advanced analytics, artificial intelligence (AI), and automated back-office processes), the advancements will change the way companies work.
In its earlier reports, Deloittehad predicted that the top five skill sets that would increase significantly in the coming years because of automation and technological advancements: computer skills, digital expertise, sound knowledge of programming for robotic applications/automation, knowledge on working with tools and technology, and critical thinking.
Secure Your Next Top
Executive Today!
ESG and DEI: Why They are Important in Manufacturing
Understanding what is ESG and why it is important, as well as why DEI is important, is crucial for modern manufacturing leaders. Their incorporation in mainstream functions has taken talent acquisition and skill enhancement to a different level. It is imperative for the leadership to maneuver talent strategy along these parameters.
Why is ESG/DEI important?
Growing regulatory pressure is one aspect. The other factor is the increasing realization of companies that ESG matters more than ever before. Events such as the global health crisis created by the pandemic, climate change and environmental issues, and social unrests underline the significance of commitment to ESG matters.
Organizations need to adopt a holistic approach to build their credential as a conscientious entity. Whether it is responsible environmental behavior, or promoting worker safety and well-being, or deciphering progress on DEI, they need to make the right effort.
Amid the growing social and environmental consciousness, ESG/DEI initiatives are critical to connect with the sentiment of the different stakeholders. These could be investors, clients, or your current and future employees.
These programs are also relevant to retain and attract talent. Millennials and Gen Zs, especially, gravitate towards organizations with a sound ESG track record.
To give effect to the program or initiative, you need dedicated roles and positions at C-suite level, with a proper infrastructure of department with other designations. These must be manned by people with the required skill and experience.
Strategizing talent acquisition for evolving skills in manufacturing: A leader’s guide
Manufacturers need to address the challenge of filling current openings and prepare their workforce for future-ready skills in manufacturing. This means adopting a holistic and dynamic talent management approach to talent acquisition, which factors in digitization, automation, and sustainability for skill transformation. An effective talent sourcing strategy is key, ensuring that the talent pool aligns with the evolving trends in manufacturing, including the increasing importance of ESG and DEI. This approach prepares the workforce to be agile and competent in the face of rapid technological and social changes.
Assess the scenario. List the changes you seek to bring. Which technologies or processes are you targeting from this perspective? How will this affect the workforce in these functions?
Assess your existing workforce. Profile them. Map their skill set, size and demography against industry standards to gauge their level of technological advancement. How do they fare against industry standards? How would digitization affect them?
Look around. How have your peers executed automation/digitization? You need not replicate, for every requirement is unique. Understand trends in the industry. What is the impact of digitalization—both qualitative and quantitative?
Follow the same process for enumerating skills from ESG/DEI perspective. What are the industry standards? What do regulations say? Can you map your existing workforce against these requirements?
On this basis, proceed with your plan.
Take your team in confidence. Given the enormity and gravity of digitization, it cannot be executed in isolation from consultation. Automation will lead to workforce reduction. This could be a pain point. Hold honest and transparent discussions about how you want to restructure processes or rethink the work architecture. Focus on how you can add value through automation, beyond workforce reduction and cost-cutting.
Hold discussions about how adding ESG/DEI angles will add value, and why is this a necessity? Take suggestions on how to proceed.
Will these initiatives result in a meaningful engagement of workers? Will these measures bring value to your customer? Explain your stand and factor in others’ views for consensus building.
Check with other department heads, HR leaders to shortlist the skills that need to be added/acquired, and phase out the ones that are redundant. Exploring the skills required in line with your technology/social strategy objectives is essential to assess the impact of pursuing automation/ digitization and social commitment on the organization.
While prioritizing the skills, factor in the skill sets that will have the biggest impact and affect the largest number of workers. Start with the broader skills and then narrow down to the highly specialized skill sets.
Once you’ve understood your skill requirements, map these against the skills available in your current workforce. This will reveal the gap that need to be filled. While expanding skill set, you could cover new soft skills, such as complex problem-solving, critical thinking, people management, creativity, decision-making, service orientation, cognitive flexibility.
Assess the scale and capability of your HR operations and training infrastructure. Discussions will also give insights into the willingness of the existing employees to accept and adapt to the changes.
Ideate on developing the delivery mechanism. Also, discuss the digital tools you would want to have, in line with the requirements.
Decide the new roles you would want to add to the C-suite. Will you need a Chief Digital Officer for automation, or will the existing CIO handle it? Which other positions will you need to create? What will be the reporting structure, roles and responsibilities?
Likewise, for ESG/DEI, who will overlook the initiatives? Existing HR, or will there be dedicated positions to handle the responsibilities, such as Chief ESG Executive/Chief ESG officer?
(The new generation of the workforce is conscientious about social commitment. They are attracted to companies with a clear social agenda, besides professional growth prospects. According to data cited in a March 2022 article by SmartIndustry, an IoT business magazine, manufacturing executives increasingly recognize that issues such as diversity and balanced gender representation are likely to expand the talent pool. When powertrain manufacturer Cummins appointed Jennifer Rumsey as CEO and President in August 2022, it made quite a splash.)
While leaders are working to foster a fair and inclusive environment, a lot needs to be done.
Aligning with your team on all these aspects will set the course for skill diversification and talent acquisition in manufacturing. They need to buy in for the strategy to be effective.
Communicate with the workforce. No transformation can be achieved in the absence of communication. You need to convince the workforce to see the value in the transition – the career growth prospects it affords, relevance to existing demands, and the efficiency it will bring.
Extremely important—how are you planning to compensate the ones affected adversely by the transformation? Seeing them go will be a sore point for their peers. If you treat the exiting employees respectfully, it will have a positive impact on employee retention and attraction.
Urge other C-suite members and practice/team leads to communicate with their respective teams and explain the management’s standpoint. You could also address the teams, depending on the size and scale.
Robust communication strategy is integral to any transition.
Get it right with Executive search and Industrial Recruitment. Given the significance of leadership and the scale of the drive, the ideal solution is to hire the services of a talent acquisition expert, such as those specializing in Industrial Recruitment. These executive search recruiters specialize in finding C-suite executives for hard-to-fill, critical roles in the industrial sector. They provide bespoke services, including retained search, contingent search, and talent advisory, which can be crucial for manufacturing companies looking to adapt to the rapidly changing skills landscape.
They have a sound understanding of the talent market across regions, with access to a large talent pool. Tapping into their holistic research-backed view of the talent landscape, combined with compensation benchmarks, you can choose the right candidate.
They use proprietary tools and techniques to provide incisive insights and valuable solutions. This includes a detailed framework to identify and recommend apt talent best suited to lead the way forward. These firms can capture deep insights into the competencies, personality, leadership traits, key drivers, and cultural fitment of the candidates, backed by in-depth market knowledge and references.
Using their experience in building inclusive leadership teams, safe and supportive workplace environments and cultures, you can build a sound DEI/ESG framework in your organization. You can also create and implement comprehensive sustainable DEI strategies to acquire and develop diverse leaders.
Play on your strengths. The other alternative to external sourcing is developing people within the organization.
Your workforce strategy should start by assessing how you can optimize the talent pool. How will you engage with it?
Consult the different division or practice heads to know which processes to focus on at the start. Decide which technologies you will use to assess the talent pool and expand the critical skillset.
Up-skilling/re-skilling can be used for both leadership development and skill enhancement.
Increase the shelf-life of skills. Build a sound framework for learning & upgrade, including re-skilling/up-skilling, along:
- Leadership development
In the rapidly evolving landscape of manufacturing, leadership development is a cornerstone for navigating through the new skills paradigm. It’s essential for manufacturing leaders to cultivate future-ready leadership that can adeptly respond to the dynamic changes in technology and workforce needs. Start with preparing a profile of the candidates with high potential available internally. So, if you are looking from ESG/DEI or sustainability leadership perspectives, decide the parameters for shortlisting the high potential candidates from your workforce. Do they have previous experience in this field? Do they have in-depth knowledge of concepts? How abreast are theywith the latest developments?
Next, decide on the solutions.
One option is to employ advanced technologies, such as immersive simulation techniques, entailing the use of AR/VR, to create virtual environments for effective training. The technologies create an immersive and “safe” environment. The new generation of the workforce relates more to advanced technologies. They are effective for many training programs, including soft skills and confidence-building.
The other is more direct. Connect with exec search firms that specialize in coaching and leadership development. If generating leaders from the internal base is difficult, you could also avail the services of these firms to source the desired candidates. - Skills other than leadership development
In the context of trends in manufacturing, it’s crucial to focus on skills beyond future ready leadership. This includes nurturing a workforce that is adept in dynamic talent management and possesses a diverse array of skills essential for the manufacturing sector’s growth and adaptability. As per the World Economic Forum, over 50% of the workforce will need upskilling by 2025 for developing the skills robots cannot perform. These include certain types of problem solving, critical thinking, and creativity skills.
Re-skilling, depending on the scale, would be cost-effective as well. Research by Wharton School of Business shows that re-skilling costs nearly 20% lesser than external hiring. - Resource availability
You may need to provide employees (depending on the requirement) access to courses on digitization/automation to social commitment-oriented, such as DEI/ESG. Consider tying up with institutes or organizations providing relevant courses across levels, from graduates to different levels of workers. For example, in its March 2022 article, Manufacturing USA, a network of technology-focused institutes that provide workforce development programs, highlights the significance of workforce development as new careers are defined around robotics, automation and AI. As a leader, you need to facilitate learning under overall career development and growth.
The perception of manufacturing is changing from its earlier image of a dirty and mechanical job. It is drawing Gen Z and millennials who are attracted to technology and digitization. You can build on this by showcasing the prospects for learning and growth. - Delivery and supervision
How will you implement your training/learning program? Will it be interactive, demonstrable or instructor-led classroom format?Decide the approach based on the complexity of skills.
If the scale and intensity of the training program is big, consider having a separate division or wing, or a nodal authority, to run and supervise it. Assuming resources permit, you could start small with a company-level training academy.
For example, Tata Steel’s plant in Ijmuiden, the Netherlands. The company’s training institute, Tata Steel Academy, determines competencies and qualifications for the employees, and designs training programs. Its educational initiatives include lessons on how to make hydrogen for secondary school students in the region. This is part of its switch to green steel initiative under sustainability in production.
Such efforts go beyond providing just targeted training. They are aimed at spreading awareness among employees—education facilitates transition.
The supervisory authority can enrich the reskilling-upskilling program. Revise it from time to time, upgrade it, add new modules and skill sets; keep a track of the people to be shortlisted for training; set the benchmarks and track performance against it. This will make the system agile.
To conclude
Talent acquisition and enhancement in manufacturing is at an inflection point. Technological advancement and social commitments have changed the paradigm of talent strategy.
Building the right workforce is less about sourcing candidates from the domain only. It has gone beyond to incorporate societal aspirations.
This changes the very premise of talent strategy. Skill enhancement and talent acquisition help to strengthen the relationship between an organization and its people. As much as manufacturing companies assess what the workforce can offer, they will be assessed on what they offer to the workforce. Every move from deciding to employ automation, reducing the workforce, scaling up employees to diversifying skill acquisition, will be watched.
The manufacturing leadership, therefore, needs to offer strong value propositions pertaining to skill transition. This will motivate its current workforce to develop new skills. Given the ricochet effect, this will draw external talent for hard-to-fill, specialized roles.
Talent strategies in manufacturing are strongly linked to changing perceptions about the industry. To deliver the transformation, the manufacturing leadership needs to take a 360-degree view on overcoming labor challenges, including societal perception management.
The days of myopic talent acquisition are over.